پودر آلومینا برای تولید بسترهای مدار مجتمع، لامپهای بخار سدیم با فشار بالا، نگهدارندههای کاتالیست، ابزارهای برش، مواد مقاوم در برابر حرارت و سایش و مواد محافظ در سیستمهای رادیواکتیو استفاده میشود. استفاده متداول از آلومینا و سایر پودرهای سرامیکی، برای تولید قطعات سرامیکی است. خواص مورد نیاز قطعات تولیدشده، وابستگی بسیار بالایی به کاربرد و نوع پودر مواد اولیه دارد. برای اکثر کاربردهای پیشرفته سرامیکی، خلوص پودر، اندازه متوسط ذرات، توزیع اندازه ذرات و شکل ذرات خواص نهایی قطعات را تعیین میکند.
خلوص پودر آلومینا بهشدت بر خواصی مانند استحکام، مقاومت در برابر اکسیداسیون و عمر تنش خستگی تأثیر میگذارد. ناخالصیها نقش مهمتری در تعیین خواص الکتریکی، مغناطیسی و نوری دارند. این ویژگیها معمولا با دقت برای یک کاربرد خاص با افزودن دقیق و کنترلشده یک ماده ناخالص، سفارشی میشوند. تغییرات کوچک در غلظت یا توزیع ماده ناخالص یا وجود ناخالصیهای نامطلوب میتواند خواص را بهطور قابلتوجهی تغییر دهد و باعث عملکرد نامناسب قطعات شود.
برای آشنایی با ویژگیهای پودر آلومینا تولید شده توسط شرکت سرام پودر از صفحه آلومینا دیدن فرمایید.
اندازه متوسط ذرات بهشدت بر خواص قطعه تمامشده تأثیر میگذارد. ذرات کوچک، برای ساخت قطعات با استحکام بالا مورد استفاده است. اندازه ذرات همچنین بر دما و زمان لازم برای تفجوشی تأثیر میگذارد. بهطورمعمول، هر چه پودر آلومینا ریزتر باشد، دما و زمان لازم برای متراکمشدن کمتر میشود. این میتواند تأثیر مهمی بر استحکام داشته باشد زیرا زمان تفجوشی طولانی منجر به افزایش رشد دانه و استحکام کمتر میشود.
برای دستیابی به حداکثر استحکام و استحکام قابل تکرار، توزیع با اندازه ذرات کوچک مورد نیاز است. ذراتی که بهطور قابلتوجهی بزرگتر از سایر ذرات هستند، میتوانند به عیبهای مهمی تبدیل شوند که استحکام قطعات تولیدی را کاهش میدهند. بهطورمشابه، حفرههای بزرگ ناشی از توزیع نامناسب اندازه ذرات ممکن است در طول پخت از بین نرود و منجر به عیبهای محدودکننده استحکام قطعات تبدیل شوند.
شکل ذرات نقش مهمی در تولید قطعات سرامیکی دارد. آگلومرهها، کلاسترهای ذرات ذوبشده، بسیار نامطلوب هستند، زیرا منجر به کاهش چگالی قطعات خواهند شد و درنتیجه این موضوع باعث عدم دستیابی به قطعاتی با خواص مطلوب خواهد شد. برای دستیابی به یک قطعه سرامیکی با کیفیت بسیار بالا، پودر آلومینا باید دارای خلوص شیمیایی بسیار بالا، اندازه ذرات ریز، توزیع اندازه ذرات کوچک و فاقد آگلومره باشد.
مشخصات پودر آلومینای تجاری در دسترس
پودر آلومینا بهصورت تجاری با استفاده از فرآیند بایر تولید میشود که در آن هیدروکسید آلومینیوم از سنگ معدن بوکسیت استخراج میشود. خلوص هیدروکسید تقریبا 5/99 درصد است که ناخالصیهای اصلی Na2O ،Fe2O3 SiO2 و TiO2 است. هیدروکسید بهطورکلی دارای اندازه ذرات متوسط 10 میکرومتر و توزیع اندازه ذرات وسیع با محدوده 1/0 تا 60 میکرومتر برای هیدروکسیدهای آسیابشده تجاری است. برخی از آلومیناهای کلسینهشده حاصل از هیدروکسیدهای بایر، خلوص بالاتری دارند. بهعنوان مثال، آلومینای کلسینهشده آلکو 16- A، دارای خلوص 7/99 درصد است. بااینحال، توزیع ذرات آن نیز بسیار گسترده و در محدوده 1/0 تا 3 میکرومتر و با اندازه متوسط 5/0 میکرومتر است. علاوهبراین، شکل ذرات کروی نبوده و بهصورت نامنظم و چندوجهی هستند که این موضوع در شکل زیر قابل مشاهده است.
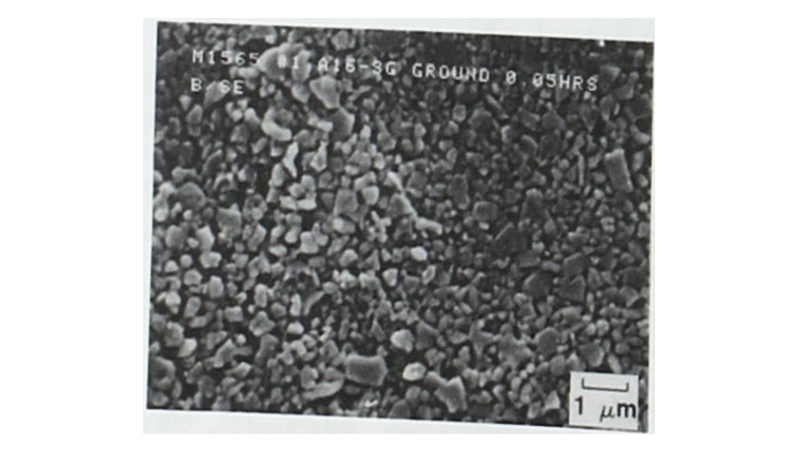
روش متداول برای تولید پودر اکسید آلومینیوم با اندازه ذرات کمتر از 1 میکرومتر، آسیابکردن این پودر و به دنبال آن، دانهبندی است. از مزایای این فرآیند میتوان به سادهبودن، کاربرد وسیع و تولید پودرهای بدون آگلومره، اشاره کرد. بااینحال آسیابکردن و دانهبندی پودر آلومینا، چندین معایب دارد: (1) محصول ممکن است در طول آسیابکردن توسط دیواره و گلولههای آسیاب آلوده شود (در حال حاضر بدنه و گلولههای آسیاب با خلوص کافی و مقاومت سایشی بالا، در دسترس نیستند). (2) اکثر طرحهای آسیاب و دانهبندی، توزیع اندازه وسیعی را تولید میکنند. (3) آسیاب و دانهبندی کمتر از 1 میکرومتر، معمولا روشی گرانقیمت است و به مصرف انرژی بالایی نیاز دارد. (4) ذرات آسیابشده هرگز بهصورت کروی نخواهد شد و شکلی نامنظم خواهد داشت. (5) در روش آسیاب، اضافهکردن مواد دوپنت نیز به هرگز امکانپذیر نبوده و نمیتوان مواد دوپنت را در این روش به پودر آلومینا اضافه کرد.
بدون دیدگاه