ماده اولیه فیوزدآلومینای سفید، آلومینای کلسینهشده است که اکسید سدیم ناخالصی اصلی آن است. تولید این ماده در مقیاس بزرگ توسط جپسون و ساندرز آغاز شد. از کورههای بلوکی برای تولید این نوع از فیوزدآلومینا استفاده میشود. کورههای ریختهگری پیوسته نیز در حدود سال 1944 توسط ریدوی و ون درپیل ساخته شدند. کورههای بلوکی بهندرت از ورودی انرژی 1500 کیلووات تجاوز میکنند، در حالی که کورههای پیوسته به ورودی 6000 کیلووات میرسند. مذاب کورههای پیوسته در قالبهای چدنی با ظرفیت 140 کیلوگرم ریخته میشود. در دهه 1960، قالبهای بزرگتر، ابتدا از فولاد و سپس از فلز آلومینیوم، برای مولایت ساخته شد. از همان قالبها برای فیوزدآلومینای سفید استفاده میشود. قالبهای آلومینیومی خنکشونده با آب از اهمیت ویژهای برخوردار هستند زیرا شمشهایی با سطوح فاقد لکههای آهن ایجاد میکند.
در تولید فیوزدآلومینای سفید، مشکل اصلی بهدستآوردن شمشهای سفید، بهطور مداوم است، زیرا فیوزدآلومینای سفید یا خاکستری به دلیل وجود ناخالصیهایی مانند کربن، آلومینیوم فلزی، گوگرد و اکسیدهایی مانند Fe2O3، SiO2 تشکیل میشود. وزنیاک فیوزدآلومینای خاکستری را در محلولهای خورنده و اسید سولفوریک، به فیوزدآلومینای سفید تبدیل میکند.
مستنداتی وجود دارد که مطابق آنها سفیدی فیوزدآلومینا را میتوان بهبود بخشید. یکی از این مستندات توسط مکزورا، گیتزن و همکارانشان بیان شده است که از افزودن آلومینای کلسینهنشده، حاوی H2O کریستالی تا 5/2 درصد استفاده میکنند. همچنین اسمنت و همکارانش ادعا کردند که افزودن مقدار بسیار کمی از رزینهای ترموپلاستیک و هیدروکربنی، رنگ سفید این نوع از فیوزدآلومینا را بهبود میبخشد.
ناخالصی که بیشترین تأثیر را بر خواص سایشی این ماده میگذارد، اکسید سدیم است که منجر به تشکیل بتاآلومینا با فرمول شیمیایی A12O311 . Na2O میشود. این در حالی است که سختی موس بتاآلومینا 7 – 5/6 است و از طرف دیگر سختی موس آلفا آلومینا برابر با 9 است که حضور این فاز در فیوزدآلومینای سفید، خود نشاندهنده کاهش میزان سختی از 9 به 7 است. ریدوی و همکارانش دریافتند که افزودن 5/0 درصد Na2O به آلومینایی که از قبل حاوی مقداری از این اکسید است، 5 تا 7 درصد بتاآلومینا تولید میکند. Na2O به دلیل فراربودن، تخلخل را در فیوزدآلومینای سفید افزایش میدهد.
در یک شمش بزرگ، Na2O در مرکز قسمت بالای آن متمرکز میشود و آن را میتوان تا حدی با جداکردن بخش مرکزی بالا حذف کرد. توزیع Na2O در شمش در شکل زیر نشان داده شده است.
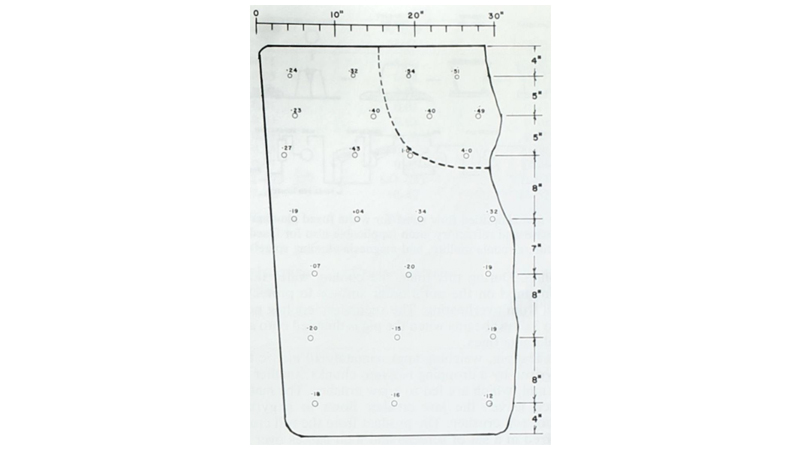
در طی خردکردن شمش، بخش غنی از Na2O که دارای فاز بتاآلومینا است، به دلیل سختی کمتر به اندازههای کوچکتر تبدیل میشود. خردههای بزرگتر از نظر آلفاآلومینا غنیتر هستند.
مراحل تولید فیوزدآلومینای سفید
مراحل تولید فیوزدآلومینای سفید در شکل زیر نشان داده شده است. یک کوره معمولی بلوکی شامل یک دیگ فولادی از نوع هاچینز خنکشونده با آب، دارای قطر و ارتفاع متوسط تقریبا 1830 میلیمتر است. دیواره فولادی با ضخامت 25 – 20 میلیمتر توسط آب جاری در سطح بیرونی آن از گرمشدن بیشازحد، محافظت میشود. الکترودهای گرافیتی (با قطر 250 – 200 میلیمتر) برای کاهش آلودگی حمام استفاده میشود. دیگ که بر روی یک پایه انتقال قرار میگیرد، در زیر دو الکترود باقی میماند تا زمانی که از مذاب پر شود. سپس در مسیرها به ایستگاه خنککننده اولیه برای 16 – 12 هدایت میشود. در طول این مدت، جریان آب خنککننده در سطح بیرونی دیگ حفظ میشود تا از گرمای بیشازحد محافظت شود. دوره سردشدن ثانویه (2 تا 3 روز) زمانی شروع میشود که شمش روی بستری از ذرات آلومینا تخلیه میشود. شمش با وزن تقریبی 10 تن، توسط ضربات گلوله به قطعات کوچکتر از 400 میلیمتر شکسته شده و به یک سنگشکن فکی وارد میشود. مادهای که از سنگشکن فکی خارج میشود به سمت یک سنگشکن چرخشی یا غلتکی هدایت مییابد. سپس ماده حاصل مشبندی میشود و از جداکنندههای مغناطیسی با شدت بالا عبور میکند. عملیات مغناطیسی باید بسیار کامل باشد تا تمام آهن جمعشده در طول فرآیند حذف شود. محصول نهایی در اندازه مطلوب، به کارخانههای تولید چرخ سنگزنی و سایندههای روکششده ارسال میشود.
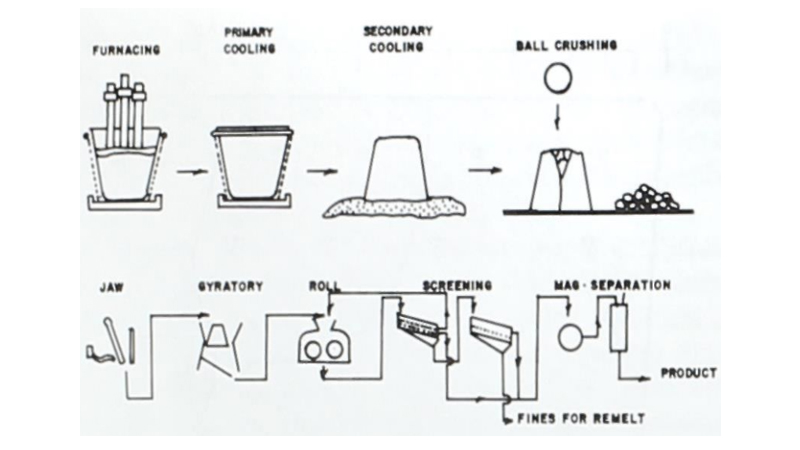
خواص و کاربردهای فیوزدآلومینای سفید
فیوزدآلومینای سفید تقریبا فاقد TiO2، SiO2 و غیره است و خواصی نظیر سختی بالا، شکنندگی با خلوص بالا، پایداری شیمیایی، نقطه ذوب بالا است. نقطه ذوب این ماده در حدود 2500 درجه سانتیگراد است. فیوزدآلومینای سفید ساینده، عمدتا با پیوندهای شیشهای برای کاربردهای سنگزنی اتاق ابزار استفاده میشود. ذرات این نوع از فیوزدآلومینا، بسیار شکننده هستند و سریعتر از ذرات فیوزدآلومینای قهوهای ساییده میشوند. شکنندگی ذرات این ماده، سبب محبوبیت آن برای استفاده در برش سرد شده است و آن را برای سنگزنی دقیق آلیاژ و فولاد با سرعت بالا و عملیات حرارتی که معمولا برای ساخت ابزار استفاده میشود، ایدهآل میکند. این ماده برای افزایش مقاومت سایشی لعاب کاشی و سرامیک نیز استفاده میشود و در صنایع نسوز نیز کاربرد دارد.
بدون دیدگاه