فیوزآلومینا به دلیل ترکیب (مقدار آلومینا و نوع و مقدار اکسید آلیاژی) و اندازه کریستال متفاوت (که تابعی از نرخ انجماد مذاب هستند) دارای انواع مختلفی است که عبارتند از: (1) قهوه ای (2) سفید (3) صورتی و یاقوتی (4) تک کریستالی (5) آلومینای اصلاحشده با مقادیر مختلف زیرکونیا، بهعنوان مثال 10، 25 و 43 درصد و (6) مشکی. جدول زیر، ترکیب مواد خام مورد استفاده و برخی از خواص فیزیکی، بهعنوان مثال، سختی و شکنندگی انواع فوق را نشان میدهد. دمای ذوب بالای آلومینا، آن را به یک ماده نسوز خوب تبدیل میکند و به محض شناسایی آن بهعنوان یک ساینده، تولیدکنندگان کاربرد آن را در زمینه دیرگداز گسترش دادند.
فیوزآلومینای ساینده
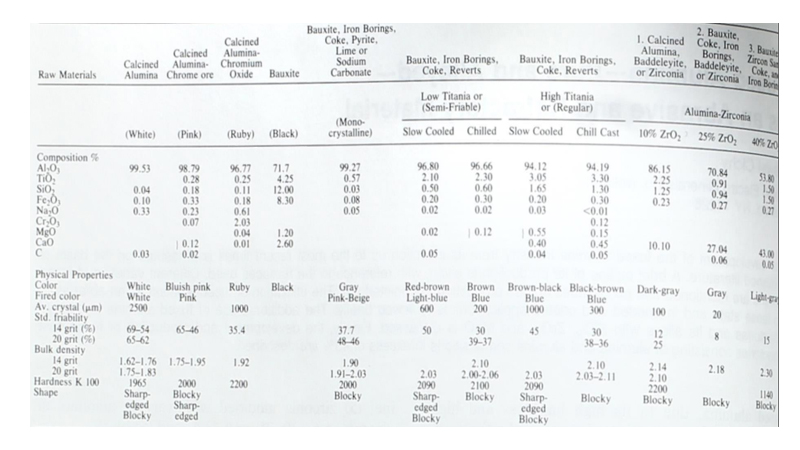
مواد خام مورد استفاده برای تولید فیوزآلومینا
ماده اولیه همه انواع فیوزآلومینا بهطور مستقیم یا غیرمستقیم، بوکسیت است. دو نوع بوکسیت اصلی یافت میشود: (1) نوع بوهمیتی یا Al2O3 . H2O و (2) نوع گیبسیتی یا Al2O3 . 3H2O. آب کریستالی و آزاد موجود در سنگ معدن استخراجشده میتواند بیش از 40 درصد باشد. این میزان آب بالا، بوکسیت خام را به یک ماده نامطلوب برای کورههای ذوب با دمای بالا تبدیل میکند. پس از آن بوکسیت باید کلسینه شود. پس از خردکردن بوکسیت خام در اندازه کمتر از 50 میلیمتر، آن به درون کورههای دوار با دمای کاری 1100درجه سانتیگراد تغذیه میشود تا محتوای کل آب را به 1 درصد یا کمتر کاهش دهد. هرچقدر مقدار آلومینای موجود در بوکسیت بیشتر باشد، بوکسیت مطلوبتر است. با افزایش مقادیر ناخالصی، انرژی مورد نیاز به ازای هر واحد فیوزآلومینا افزایش مییابد. بر اساس تحقیقات والکر، با افزایش ناخالصیهای SiO2، Fe2O3 و TiO2 انرژی مصرفی افزایش مییابد. مقدار CaO و MgO در بوکسیت برای هر کدام، باید بیشتر از 4/0 درصد باشد. بهجای بوکسیت کلسینهشده، میتوان از بوکسیت زینترشده استفاده کرد که بهرهوری انرژی در عملیات ذوب را بهبود میبخشد.
برای ارتقاء بوکسیت از مقدار اکسید آلومینیوم 87 – 85 درصد به حدود 97 – 96 درصد در تولید فیوزآلومینای قهوهای، از عوامل احیاکننده مانند کک و آنتراسیت برای کاهش اکسیدهایی مانند Fe2O3 ، SiO2 و TiO2 استفاده میشود. اگر اختلاف چگالی بین آلیاژ تشکیلشده از ناخالصیها و آلومینای مذاب به بیش از 3 گرم بر سانتیمتر مکعب برسد، ناخالصیهای فلزی تشکیلشده را میتوان بهراحتی از سرباره آلومینا جدا کرد.
ماده اولیه فیوزآلومینای سفید، صورتی و یاقوتی، آلومینای کلسینهشده است که توسط فرآیند بایر از بوکسیت بهدست میآید. محدوده ترکیب آلومینای کلسینهشده در جدول زیر نشان داده شده است.
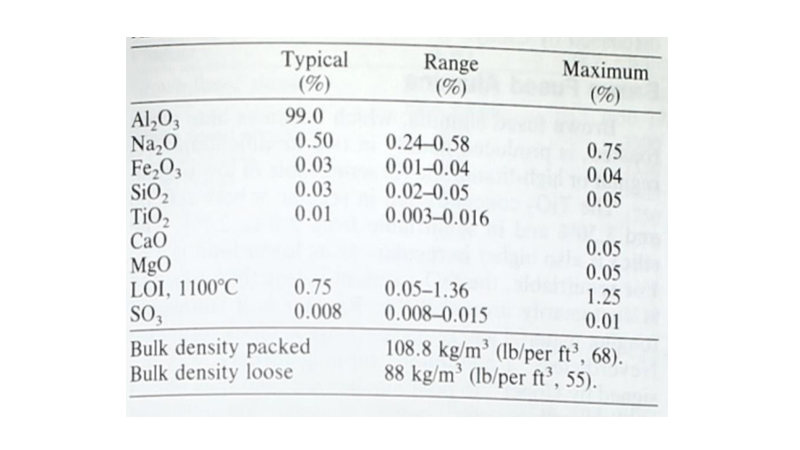
مواد خام مورد استفاده برای اصلاح خواص مواد خام ساینده و دیرگداز فیوزآلومینا عبارتند از (1) سیلیس (2) اکسید کروم یا سنگ معدن ارکروم (3) زیرکونیا یا بادلیت (4) زیرکون یا زیرکونیوم سیلیکات (5) منیزیت و (6) کیانیت و آلوزیت و سیلهمات.
کورههای مورد استفاده برای تولید فیوزآلومینا
کورههای مورد استفاده برای تولید فیوزآلومینا، از نوع قوسی هستند. مذاب جامدشده یا دراصطلاح جمجمه، مذاب را محدود میکند. بنابراین هیچ آلودگی در مذاب رخ نمیدهد. مذاب جامدشده در داخل پوستهای قرار میگیرد که ممکن است آستر باشد یا نباشد. در جایی که خطر تشکیل مذاب فلزی وجود ندارد، بهعنوان مثال، در فیوزآلومینای سفید، هیچ آستری لازم نیست. در مواردی که نمیتوان از ایجاد فلز اجتناب کرد، مانند تولید فیوزآلومینای قهوهای، پوسته توسط یک آستر گرافیت یا کربن محافظت میشود. بسیار مهم است که ضخامت جمجمه ثابت بماند تا از شکستن پوسته فولادی جلوگیری شود. بنابراین ذوب باید در شرایط پایدار انجام شود و تلفات حرارتی باید با گرمای ورودی در فصل مشترک جمجمه – ذوب برابری کند. برای حفظ یک جمجمه نسبتا نازک، پوسته فولادی توسط یک فیلم خنک می شود. بسیار مهم است که ضخامت جمجمه ثابت بماند تا از شکستن پوسته فولادی جلوگیری شود. بنابراین ذوب باید در شرایط پایدار انجام شود، جایی که تلفات حرارتی باید با گرمای ورودی در فصل مشترک جمجمه-ذوب برابری کند. برای حفظ یک جمجمه نسبتا نازک، پوسته فولادی توسط یک لایه آب جاری بر روی سطح بیرونی آن و با برخورد اسپریهایی در پایین آن خنک میشود. نوع کوره بستگی به نحوه کارکرد آن دارد. کورههای اولیه تکباری بودند. انرژی ورودی آنها حدود 1000 کیلو وات بود، بهاستثنای معدودی که به ورودی 2000 و 3700 کیلووات میرسید. برای کاهش هزینه های عملیاتی، لونزو یک کوره ذوب مداوم را در طول جنگ جهانی دوم معرفی کرد. پس از سال 1945، شرکت کاربراندم، کورههای مداوم کج را با ورودی 3500 کیلووات معرفی کرد. در ایالات متحده آمریکا، کورههای 7500 کیلوواتی تا سال 1965 کار میکردند و یک کوره 12000 کیلوواتی در حال طراحی بود. کورهها در ایالات متحده آمریکا از نوع کوبشی ثابت هستند. مذاب از طریق سوراخ واقع در قسمت پایینی پوسته کوره خارج میشود. کورههای مورد استفاده در کانادا و ایالات متحده، از نوع کج هستند که مذاب از یک دهانه در بالای پوسته کوره، از آن خارج میشود.
بدون دیدگاه