آسیابکاری مکانیکی، روشی قدیمی و رایج برای تهیه پودر وآلیاژهای پودری است که برای کاهش اندازه ذرات تا حدود دهها نانومتر مناسب است. در فرآوری مواد سرامیکی، با کاهش اندازه ذرات، نسبت سطح به حجم ذرات افزایش و با افزایش نفوذ، زینتر افزایش مییابد. این امر میتواند منجر به کاهش دمای زینتر شود. اگر دمای زینتر مورد نیاز کاهش یابد، ممکن است کاربردهای بالقوه این ماده بهطور قابلتوجهی افزایش یابد. زینتر آلومینا با فلزاتی با نقطه ذوب پایین (کمتر از دمای زینتر آلومینا که حدود 1700 درجه سانتیگراد است) مانند پلاتین، میتواند برای کاربرد در دستگاههای زیستپزشکی مفید باشد.
در آسیابکاری مکانیکی از گلولهها برای خردکردن و تبدیل مواد به پودر استفاده میشود. بدنه آسیابهای بزرگ معمولا از فولاد سختشده ساخته میشوند، زیرا در مقایسه با سایر مواد هزینه پایینی دارند. گلولهها و بدنههای آسیابهای موجود تجاری معمولا از جنس مواد مبتنی بر کاربید مانند WC و SiC و سرامیکهای ZrO2 و Al2O3 است. یک مشکل عمده در عملیات آسیابکاری، آلودگی ناشی از گلولهها و بدنه آسیاب به دلیل سختی بالای آلومینا است. اهمیت این آلودگی، بستگی به کاربرد ماده آسیابشده دارد. به عنوان مثال در آسیابهای فولادی، آلودگی ناشی از آهن وجود دارد که میتواند در ساخت برخی از جواهرات مصنوعی مانند یاقوت کبود مفید باشد ولی کاربردهای زیستپزشکی را محدود کند.
در این مطالعه که توسط کارولین بی رید و همکارانش ]1[ انجام شده است، آسیابکاری پودر آلومینا در محفظه و با گلولههایی از جنسهای مختلف، مورد بررسی قرار گرفته است تا میزان آلودگی هر یک از آنها مقایسه شود و اثربخشی آنها در کاهش اندازه کریستالیت پودرها بررسی شود.
شرح آزمایش
آزمایشها مطابق شرایط نشاندادهشده در جدول زیر انجام شده است.
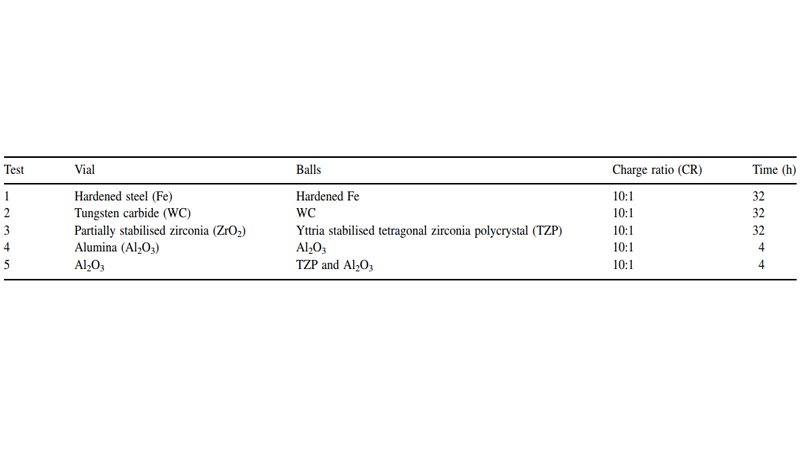
زمان آسیابکاری از طریق آزمایشهای اولیه بر روی نمونهها با استفاده از محیط آسیاب انتخابی، با هدف یافتن زمان آسیاب مشترک که با آن همه نمونهها را بتوان با هم مقایسه کرد، تعیین شده است. در این آزمایشها، نسبت گلولههای آسیاب به پودر، 10:1 و زمان آسیاب 32 ساعت انتخاب شده است. زمان آسیابکاری طولانیتر، منجر به ازهمپاشیدگی کامل گلولهها میشود. تقریبا 30 درصد از هر پودر آسیابشده در محلول HCl در حال جوش به منظور ازبینبردن آلودگی آهن، غوطهور میشود. این روش بر اساس انحلال آهن است که منجر به ایجاد یک محلول FeCl3 میشود. سپس این محلول تخلیه شده تا پودر آلومینای تمیز باقی بماند.
آنالیز XRD نمونههای حاصل از آسیابکاری مکانیکی
الگوهای XRD پودرهای آسیابشده در شکل زیر نشان داده شده است. یک پودر آلومینای آسیابنشده به عنوان نمونه شاهد در شکل (الف) نشان داده شده است که بیشتر شامل آلفاآلومینا با ساختار کوراندوم و مقدار بسیار کمی بتاآلومینا (حدود 2 درصد) میباشد. تجزیه و تحلیل عنصری XRF عدم وجود هرگونه آلودگی قابلتوجهی را نشان داد. پیکهای پراش اضافی در سایر الگوهای XRD نشان میدهد که آلودگی با هر نوع آسیاب، البته به میزان متفاوتی (به غیر از آسیاب در محیط آلومینا) رخ میدهد.
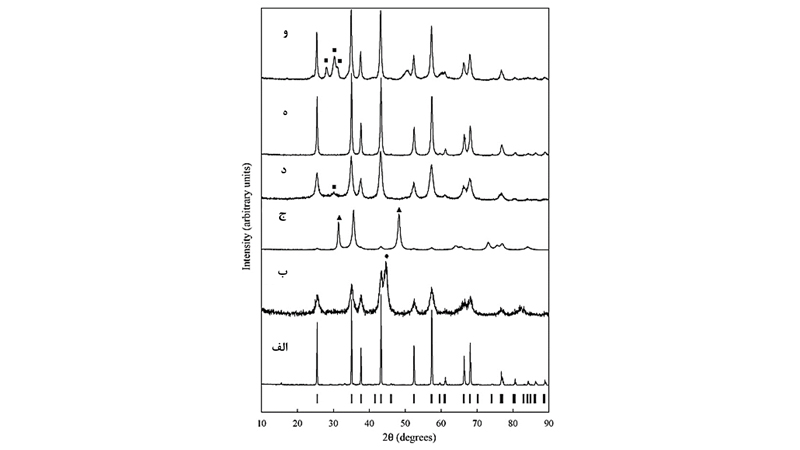
الگوهای XRD پودرهای Al2O3 حاصل از آسیابکاری مکانیکی (الف) آسیاب نشده (ب) گلولهها و بدنه از جنس فولاد سختشده (●، آلودگی Fe)، (ج) گلولهها و بدنه از جنس از WC(▲، آلودگی WC) (د) گلولهها و بدنه از جنس ZrO2(■، آلودگی ZrO2) (ه) گلولهها و بدنه از جنس Al2O3 (و) بدنه از جنس Al2O3 و گلولهها از جنس Al2O3 و ZrO2. نشانههای زیر الگوهای XRD، مربوط به h k l برای آلفاآلومینا است.
آزمایش 1:
آسیابکاری با گلولهها و بدنه آهنی، باعث ایجاد آلودگی قابلتوجه آهن در پودر آلومینا شده است (شکل فوق (ب)). پیک پراش بزرگ آهن در حدود 45=ɵ2 مشهود است. آنالیز XRF نشان داده است که در آلومینای آسیابشده به مدت 32 ساعت، تقریبا 16 درصد آلودگی آهن وجود دارد که باعث شده رنگ نمونه از سفید که مشخصه پودر آلومینا است به سیاه تغییر کند. نتیجه XRF با الگوی XRD سازگار بود (تقریبا 11 درصد از آهن کریستالی نشان داده شده است). آنالیز XRF نشان داد که این آلودگی با انحلال درون HCl به حدود 2 درصد کاهش یافته است.
آزمایش2:
آسیابکاری پودر آلومینا با گلولهها و بدنهای از جنس WC، سبب ایجاد پودر سیاهرنگ شده است که نشانهای از آلودگی قابلتوجه است. الگوی XRD (شکل فوق (ج)) نشان میدهد که سهم WC در الگو بسیار زیاد است و مطابق آنالیز XRF، مقدار آن حدود 35 درصد است. مقدار آلودگی هیچکدام از پودرها به جز پودر آسیابشده درون آسیاب آهنی، با انحلال پودر درون HCl تغییری نکرد. اندازه کریستالیت در این آزمایش با آزمایش 1، قابل مقایسه است. اندازه کریستالیت نمونهها در جدول زیر آورده شده است.
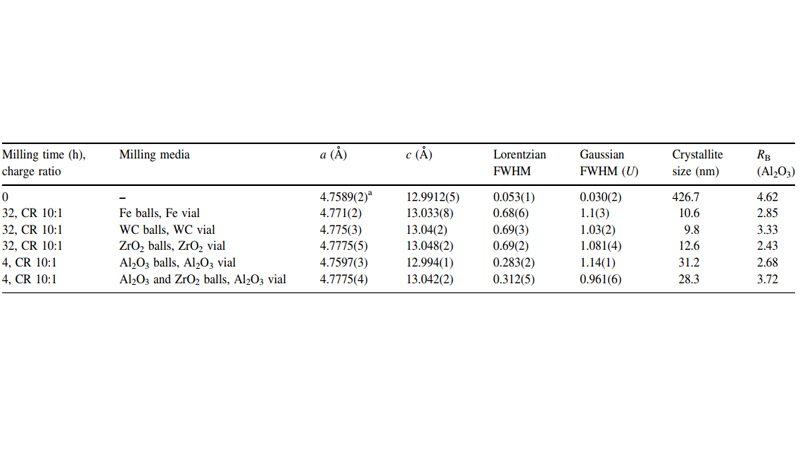
آزمایش3:
این آزمایش که در آن جنس گلولهها و بدنه از ZrO2 است، موفقترین آزمایش بر اساس آنالیز XRF برای تعیین درجه آلودگی بوده است. این آنالیز نشان داده است که پس از آسیاب، 4 – 3 درصد آلودگی از محیط ZrO2 (شکل فوق (د)) پس از آسیابکاری وجود دارد.
آزمایش4:
مطابق شکل فوق (ه))، آسیابکاری پودر درون بدنهای از جنس Al2O3 با گلولههایی از همین جنس، ناموفق بوده است. در شروع آسیابکاری، نسبت شارژ 10:1 بوده است. پس از طی 4 ساعت، وزن کل گلولهها 27 درصد کاهش یافته است و وزن پودر 438 درصد افزایش یافته است. 91 درصد از افزایش وزن پودر را میتوان به ساییدگی گلولهها و 9 درصد دیگر را نیز به تخریب دیوارههای آسیاب نسبت داد. از 100درصد پودر در پایان آزمایش، 5/62 مربوط به گلولهها، 28/22 درصد از دیواره آسیاب و تنها 7/14 درصد از پودر اولیه بوده است. اندازه کریستالیت در این آزمایش، بیشتر از سایر آزمایشها بیان شده است.
آزمایش5:
در این آزمایش که آسیابکاری در بدنهای از جنس Al2O3 با گلولههایی از Al2O3 و ZrO2 انجام شده است، از نظر آلودگی عملکرد ضعیفی داشته است. ترکیبی از گلولهها باعث افزایش تخریب در هر دو نوع گلوله شده است. تنها پس از 4 ساعت، وزن گلولهها 49 درصد کاهش یافته است. الگوی XRD (شکل فوق (و)) پیکهای پراش قابلتوجهی را در حدود 30=ɵ2 نشان میدهد که متعلق به زیرکونیای تتراگونال و مونوکلینیک است. آنالیز XRF تقریبا 5/12 درصد از این آلودگی را به ZrO2 نسبت داده است.
آنالیز SEM نمونهها
آنالیز SEM نمونهها در شکل زیر نشان داده شده است. ذرات آلومینا تیرهتر و آلودگیها روشنتر هستند. آلودگی در شکلهای (ب)، (ج) و (و) آشکارتر است: Fe، WC و ترکیبی از گلولههای Al2O3 و ZrO2. آلودگی کمتری در شکل (د) مشهود است. در شکل (ه) از نمونه آسیابشده درون آسیاب Al2O3، فقدان کنتراست نشاندهنده کمبودن مقدار آلودگی است. اما یکی از ویژگیهای قابلتوجه این نمونه وجود ذرات بسیار بزرگ است. اعتقاد بر این است که این ذرات بزرگ بقایای بدنه یا گلولههایی هستند که در طی فرآیند آسیابکاری فرسایش یافتهاند.
اندازه آگلومرهها و بزرگترین ذرات در شکل زیر قابل مشاهده هستند و در آسیابهایی از جنس Fe، WC و ZrO2 قابل مقایسه است. با این حال، نمونههای حاصل از آسیابکاری درون آسیابهای Al2O3 و Al2O3 و ZrO2 (اشکال (ه) و (و)) نشان میدهند که ذرات بزرگتر در هر دو نمونه بهطور قابلتوجهی بزرگتر هستند. لازم به ذکر است که اندازه ذرات تعیینشده توسط XRD به میانگین پراکندگی همگن ذرات اشاره دارد که ذرات با اندازههای کوچکتر بر آنها غالب خواهند بود.
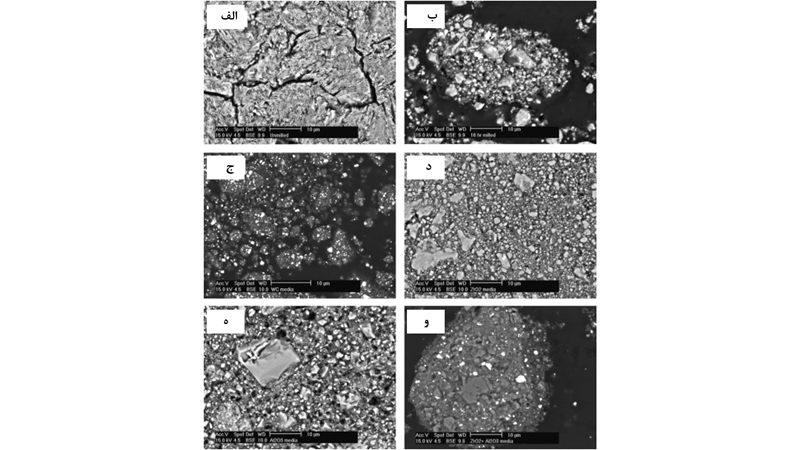
تصاویر SEM نمونههای حاصل از آسیابکاری مکانیکی (الف) ذرات آلومینای آسیابنشده و نمونههای آسیابشده (ب) در آسیاب با بدنهای از جنس فولاد سختشده (ج) در آسیابی از جنس WC (د) در آسیابی از جنس ZrO2 با گلولههای ZrO2 (ه) در آسیابی با بدنه و گلولههایی از جنس Al2O3 (و) در آسیاب Al2O3 با گلولههایی از جنس ZrO2 و Al2O3.
نتایج ریتولد نشان میدهد که آلودگی ایجادشده در آسیابی از جنس ZrO2 در مقایسه با سایر آسیابها بسیار کمتر (حدود 4 – 3 درصد) است که این امر به چند دلیل حائز اهمیت است:
- مقدار کم آلودگی، تاثیر کمتری بر خواص آلومینا خواهد داشت.
- ZrO2 در آلومینا محلول نیست و پودر حاصل هنگام زینتر نباید تغییر رنگی داشته باشد (ارزش در بازاریابی محصولات).
- مقدار سایش گلولههای آسیاب و بدنه آن بهطور قابلتوجهی کمتر است و درنتیجه طول عمر آسیاب را طولانی میکند.
- ZrO2 دارای خواص مکانیکی بهتری نسبت به آلومینا است (به عنوان مثال چقرمگی شکست و استحکام کششی بالاتر). افزودن ذرات پراکنده ZrO2 میتواند آلومینا را پس از زینتر تقویت کند.
همانطور که گفته شد HCl آهن را در خود حل میکند. استفاده از HCl برای تمیزکردن سایر نمونهها ناموفق بود. ممکن است راهی برای تمیزکردن آلومینای حاصل از آسیابکاری مکانیکی از سایر آلایندهها مانند ZrO2 وجود داشته باشد، اما در مورد ZrO2 این احتمال وجود دارد که حلال ZrO2، Al2O3 را نیز در خود حل کند. ممکن است افزودن درصد کمی از ZrO2 به آلومینای آسیابشده بتواند به کاربرد آن در مصارف زیستپزشکی کمک کند.
استفاده از آسیاب Al2O3 نیز مشکلات خاص خود را دارد. سختی بالای بدنه آسیاب و پودر و چقرمگی شکست کم آلومینا به این معنی است که گلولهها و بدنه آسیاب بهسرعت فرسایش مییابند و دستیابی به ذراتی با اندازههای نانو دشوار است، زیرا ذرات بزرگ آلومینا بهطور مداوم از بدنه و گلولهها به پودر آلومینا اضافه میشوند.
الککردن پودرها پس از آسیابکاری، ذرات بزرگ آلومینای ناشی از سایش بدنه آسیاب را از بین میبرد. با این حال، طیفهای EDS نشان دادهاند که آلودگیهای ناشی از بدنه آسیاب Al2O3 پس از الک نیز دارای مقادیر کمی ZrO2 هستند که احتمالا در هنگام تولید بدنه آسیاب استفاده شدهاند. درواقع، آسیابکاری آلومینا در محیط آسیاب Al2O3 نیز، مشکلاتی مشابه سایر آسیابها دارد.
از منظر سختی، تنها بدنهای که قادر به آسیاب آلومینا بدون مشکل آلودگی است، ممکن است الماس زینترشده و مواد مشابه الماس (مانند cBN) باشد. هر چیزی که نرمتر از آلومینا باشد، توسط پودر آلومینا ساییده میشود. اینکه آیا این دو ماده میتواند نسبت به سایر مواد مزیتی ایجاد کند یانه، باید مورد بررسی قرار گیرد، زیرا مقاومت در برابر سایش مواد سخت نیز توسط چقرمگی شکست کنترل میشود.
مرجع:
[1] Caroline B. Reid, Jennifer S. Forrester, Heather J. Goodshaw,
Erich H. Kisi, Gregg J. Suaning, A study in the mechanical milling of alumina powder, Ceramics International 34 (2008) 1551–1556.
بدون دیدگاه